Cotton canvas is a very common fabric, but how much do you know about it? Its history goes back to Ancient Egypt. Then, in the Middle Ages, it was used by Venetian merchants as sail cloth for tall ships during the Age of Exploration. Even now it is used in many ways, such as for bags, canvases for oil painting, tents, and building materials. Even belts worn by sumo wrestlers are made of canvas.
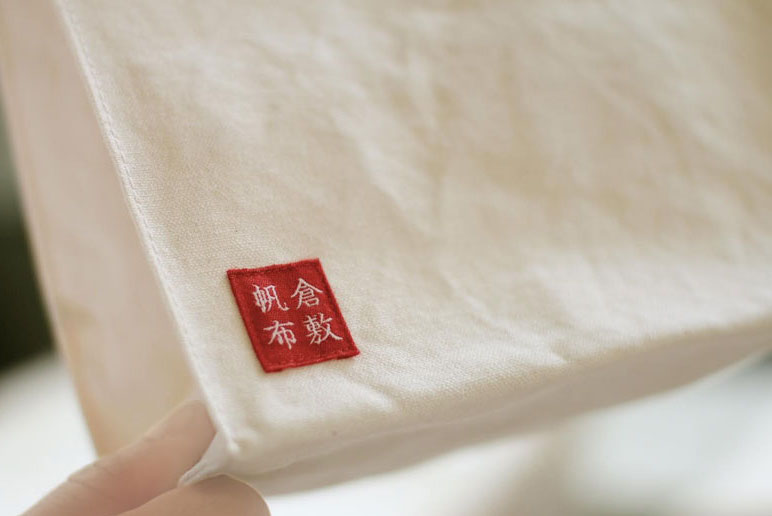
Overwhelming Chinese Production
In Japan, canvas has been woven since the late Edo era, in the 19th century, but it declined as time passed. Cheap cotton canvas from overseas countries, mainly China, began dominating the market in 1993. The price was one tenth of the price of canvas made in Japan when it entered the market, an expert of industrial canvas in Osaka recalls.
Nowadays, the amount of industrial-use canvas made in Japan doesn’t reach even one tenth of the amount produced in China. I predict that this harsh situation for Japanese manufacturers will continue for at least another decade.
Kurashiki, in Okayama prefecture, produces the most canvas in Japan. But their severe situation is not any different than everywhere else. At their peak, their production was 21.44 million m2, but now it has declined to 2.983 million m2, which is a decline of nearly one tenth (Okayama Fabric Structural Reform Association, 2014).
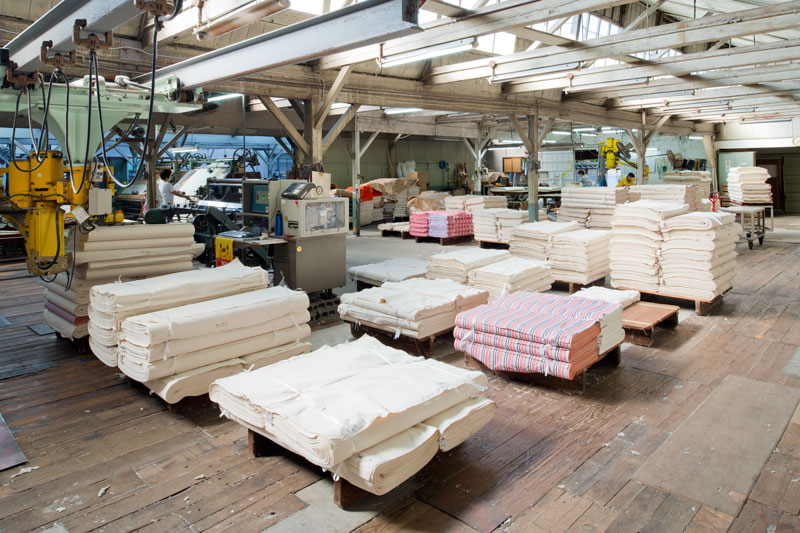
Inside Marushin Industry. Some cotton canvas produced in other countries are woven with single yarn. However, originally in Japanese Industrial Standard, cotton canvas was defined as fabric woven with two-fold yarn, and unless with two-fold yarn, it should be simply called a “cotton fabric”, says Gamou from Marushin Industry. Although Japanese Industrial Standard for cotton canvas was eliminated in 1997, Marushin strictly sticks with the standard.
Kurashiki, the City Famous for Cotton Textiles
Kurashiki, Okayama, is now famous as a denim production area, but its history of cotton fabric production goes back 400 years. In the 17th century, people in Kurashiki took advantage of their drained land, which was not suitable for rice farming, and started cotton harvesting.
However, in order to develop as a unique production epicenter that continues to today, it could not be said without their opportunistic attitude and flexibility toward the trend at the age.
Starting with the production of traditional Kimono belts and straps (Sanada-himo, Kokura-himo, and Sanada-Obi) to socks, they changed their main products from time to time depending on the market demand. While doing so, they accumulated techniques to deal with thick cotton fabrics, which lead to the production of thick cotton fabrics like canvas.
Old Shuttle Looms for Weaving
Marushin Industry has been weaving canvas here since 1933.
In contradiction to overseas companies, they do not use the latest, high-functioning looms. Instead, they stick with old shuttle looms made in the 1960s by repairing them.
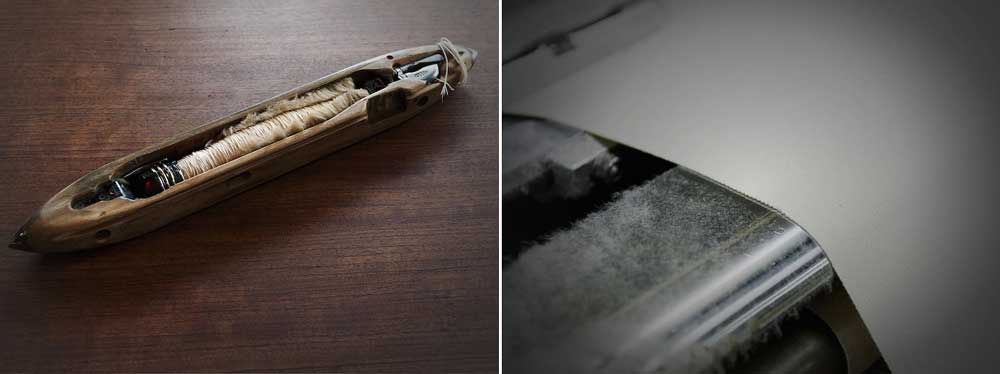
(Left) Shuttle for old shuttle looms. The name “shuttle” came from space shuttle, for it makes a “round trip” from right to left on loom.
(Right) Selvedge is another symbolic feature on fabric woven with old shuttle looms. Since canvas was mainly used for industrial materials, it needed to have strength and durability. For having selvedge, fabrics wont fray.
In terms of productivity, these looms require much more time to weave compared to the latest models. For example, the latest type of loom, a jet loom, can weave 1,000 to 1,200 meters a day, while the old model weaves only 50 to 70 meters per eight hours. Yet, Marushin values the shuttle loom for the texture and feel it produces. By weaving slowly, fabrics take in air, and the fabrics gain a soft, gentle feeling that cannot be created with mass produced canvas.
However, the old looms are no longer in production over 40 years ago. “You cannot get any parts nor any servicing”, says Noriyuki Gamou, a manager at Marushin.
Currently we have 60 shuttle-looms. We mend them and even make replacement parts ourselves. To source parts, we sometimes buy looms from other factories that closed and dismantle them because we can’t ask for any help.
When there are no more looms that we could gather from outside, we will stop 10 units at our place so that we can save them for dismantling. When even more looms get broken, we will have to quit our business.
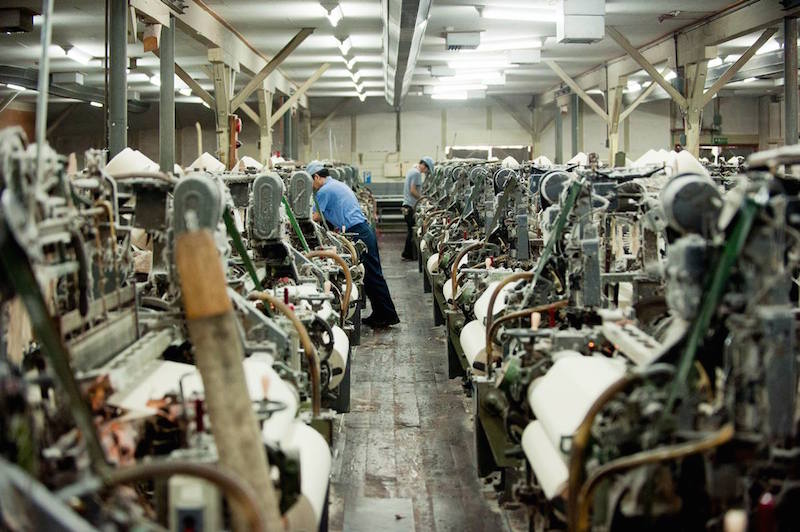
Inside Marushin Industry’s loom room. There are 60 looms working here.
Hands and Fingers Have Conversations with the Threads
One may say shuttle looms and jet looms are both machines. How are they different? We asked Tsudakoma, one of the leading loom makers.
It is solely whether there are human hands involved or not. You can see the distinguishing difference when you dye them.
These days, the latest models and old models are used for different objectives, so we cannot compare them simply. The latest models are for mass production. In factories, even the temperature and the humidity inside is completely controlled with computers in order to make products without any differences.
On the other hand, shuttle looms are operated and controlled by man. They operate looms trusting their sense and skills, which leads to slight difference in texture and faces with each final textile.
Of course the latest models also value texture. But for mass production, equality and uniformity are pursued, which results in removing unique characteristics.
The artisans say that they have conversations with textile by touching it. They touch it so much that their fingerprints fade away. Takahiko Nishinaka, the factory manager at Marushin, says that you need the sensitivity of human hands, especially when you adjust the warp yarn.
We always use our hands when we adjust yarns to warp it tight enough. We cannot make good textiles without tightly braced yarns. Indeed, once you start weaving, all you need to do is mainly to look around if it’s working right. But before that, we need to adjust the condition of the yarns according to the weather or what kind of canvas we need to make.
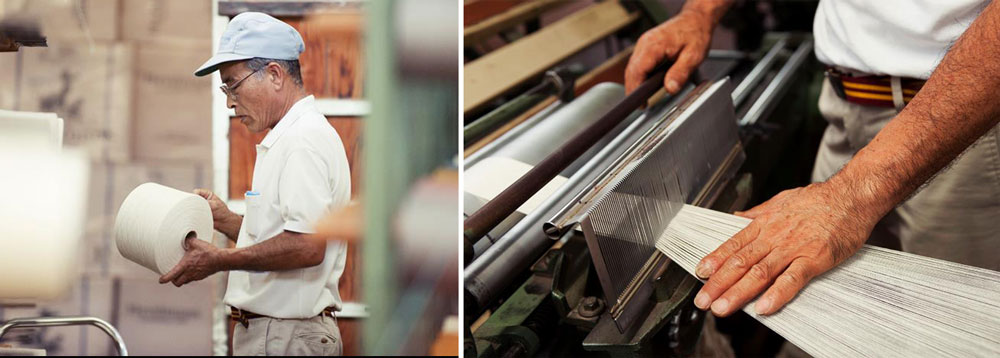
(Left) Condition of yarns slightly changes according to season’s climate and weather. Everyday, artisanal technicians touches yarns to understand the conditions and adjusts the yarn to adequate stretch.
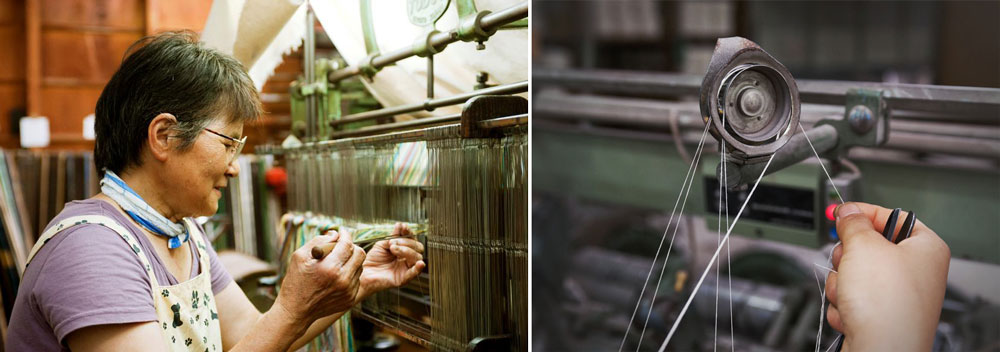
(Left) Process to prepare warp by threading the needle one by one. There are 2,000 warp on one fabric roll.
(Right) Tying yarns on yarn-doubling process.
Finding the Own Way
Marushin launched Baistone Co., Ltd. in 2003 with Takeyari Corporation, another canvas manufacturer in Kurashiki. Baistone makes end products, such as bags and chandlery, which they sell as the factory brand Kurashiki Hanpu. Gamou explains the reasons for doing this.
As the production amount declines each year, we couldn’t maintain the company only by just weaving fabric. Also, companies that produce final product had much better benefit than us fabric makers, and we didn’t even know what our fabrics would be used for. We thought we need to change our attitude and express ourselves the quality and uniqueness of the Kurashiki Canvas.
Not only designing themselves, they also collaborate with various designers (for the Kurashiki Hanpu collection) and actively show the different faces of simple cotton canvas.
They have their flagship store in Bikan district, Okayama, but they say that they would also like to focus on online advertising and sales.
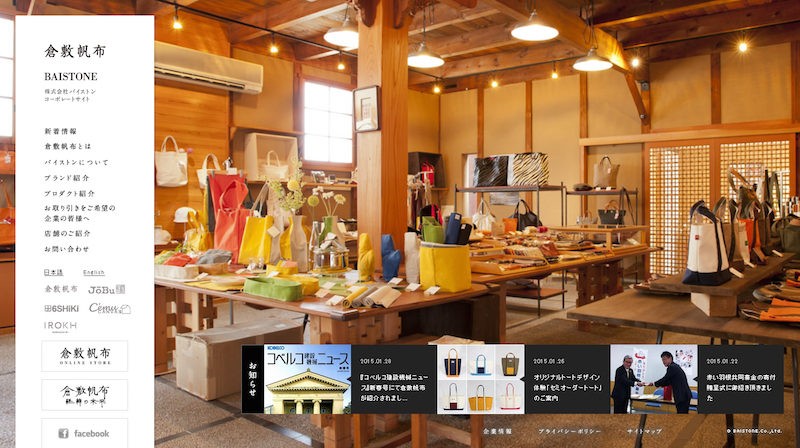
Kurashiki Hanpu Website. It gives descriptive history and process of fabric production to help customers understand deeply.
Although they adjust themselves to the modern digital society, they say they will stick with the old traditional way of canvas production: producing canvas with care and effort for each and every fabric.
Mika Takeyari, managing director of Baistone, says,
We are seeing rising demand of customization among consumers. They want something original, and we can meet that demand.
We sell fabric pieces that customers can make things themselves; it is selling very well. Also, our semi-made-to-order is gradually gaining popularity. In this service, we offer a wide variety of textiles in both thickness and color, which can flexibly meet the various tastes of each customer.
This flexibility and variation is available because of the artisans. That is why we want to share with the world via the Internet how artisans are working so hard to create or ameliorate fabrics.
But at the same time, we have to keep in mind that we are talking to an actual person, not to the digital screen. We need to sincerely care about the person for a deep and heart-touching communication.
From their vision, we can see how they are adapting to modern technology and demand while treasuring their history: the spirit of Kurashiki craftsmen that has existed since the 1600s. They were able to do that because they pay close attention to people’s voices and needs. If there are no people using the product, the history will vanish. One can turn modernization into an advantage to avoid the sad end.
(Translation by Akiko Ishige)